My Start with the LocoFi™ Locomotive Controller Board
By
Bob Lankston
January 2023
At Christmastime 1954, I was in third grade. Santa Claus gifted me a Lionel O-27 gauge trainset a couple of days after Christmas when my dad found the set at a discounted price in a store that was trying to liquidate its unsold stock of Christmas toys. By most accounts, the Lionel O-27 sets of the day were not really railroad models, i.e., they were toy trains. In my case, the toy was set out as part of my family’s annual Christmas decorations for several years. When I was in junior high school, I had a bedroom to myself. In the space that a second twin bed would occupy, the trainset was laid out “permanently” on a dedicated table approximately 4 ft x 8 ft. My dad had a job relocation when I started high school, and between moving and my adolescence, my interest in trains, whether models or toys, diminished.
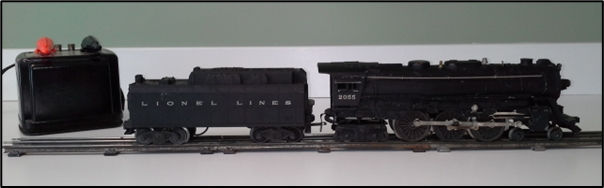
The Lionel toys were packed in a box after Christmas 1960 and stayed there until 1990 when I had my own grade school aged son. Reprising a family tradition, my son and I set out the antique Lionel equipment at Christmastime that year. Yes, those old moving boxes had seen four or five moves of my parents’ household and a couple more moves with me after my parents downsized the Lionel gear to me in the mid-1980’s. A year later, my wife and I decided to purchase a Bachmann HO scale train set for our son, or was it really for the child in me. We packed the Lionel toys into plastic storage tubs where they sit to this day.
In 1991, my son and I deployed the new HO set during the holiday season on the floor of the dining room of our house. The dining room was vacant because we had no dining room furniture in those days. The train set was reboxed and put away with the Christmas decorations after the holiday season. I learned that running the model train on the floor could lead to problems. That might have been the source of a problem that I will mention later. To avoid the dust and fibers on the carpet, when the Christmas decorations came out the next year, 1992, we placed the train layout on a 4 ft x 8 ft sheet of plywood that sat on two wooden sawhorses. The sawhorses were not very tall, and the tabletop height was better for a six- or seven-year-old than for his dad.

The trainset came out for the holiday season of 1993, again set out on the 4 x 8 board, but, this time, the components did not get packed away in January with the Christmas decorations. The layout became “permanent”, and the original set was augmented through the years with new locomotives and railcars, turnouts, buildings along industrial sidings, and trees and other scenery elements. I packed it all away in 1999.
Analogous to what had happened in my family forty years earlier, I was being transferred to a new town by my employer, and my son, who was entering high school, had interests more compelling than model railroading.
Throughout the expansion of our model train display during the 1990’s, the layout was traditional analog direct current (DC) in which the power to the locomotive and the control of the speed and direction of the locomotive were sent through the tracks, i.e., more voltage from the powerpack to the tracks made the locomotive go faster and flipping a switch to reverse the polarity of the DC power reversed the direction that the locomotive moved. By electrically isolating sections of the tracks and having two power packs, we were able to operate two DC locomotives simultaneously.
By 1999, a standardized alternative to the traditional analog DC system was beginning to enter the model train market. It was called Digital Command Control (DCC). I had heard of the system through visits to train shows and hobby shops, but I was not really interested. Through research many years later, I learned that DCC was the culmination of numerous attempts through the 40 to 50 years prior to standardize the control of more than one locomotive on a track, to provide locomotive sounds, and to control other features of a model train layout. DCC used the track to convey both power to the locomotive(s) and digital control signals for direction and speed. Actually, the Lionel set that I mentioned above used control signals sent through the AC-powered tracks to reverse the direction that the locomotive moved and to cause the whistle to blow. The 1950’s technology was basic and analog, but it worked.
DCC built on the technology available in the early 1990’s. The DCC standard for power and signal coding was defined by the NMRA in 1994. Computer to computer communications, perhaps more generically expressed as digital communications between two devices, then were by wire. Wireless, i.e., by radio, computer to computer communications did not exist when the DCC standard was defined. Wi-fi was not introduced until 1997 with Bluetooth coming along two years later. With the establishment of the DCC standard in the mid-1990’s, the big-name manufacturers in the model train market began developing products that did not use proprietary signaling schemes but products that were interchangeable with other brands. DCC has become a deeply entrenched method for model train control despite the relative antiquity of its technology.
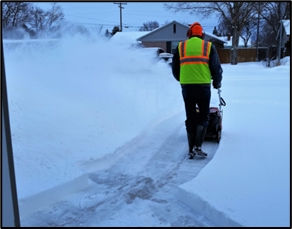
Those boxes containing the HO train layout that I packed in 1999 made three employment/retirement-related moves with me without being opened. In fact, the boxes were not opened for seven years after the last of those three moves. In the fall of 2015, something prompted me to set out some of the HO items that had been boxed up for sixteen years. I did not want the effort to be associated with Christmas, per se, and I labeled the effort my wintertime craft.
We lived in western Montana in those days, and the craft was a welcome diversion from the nearly daily shoveling of snow from the driveway and sidewalks.
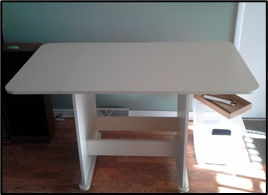
That first wintertime layout was placed on a 4 ft x 4 ft scrap of common half inch thick drywall. My wife and I were remodeling the basement in our Montana house, and that scrap was at hand. I placed the drywall panel on a drop-leaf, counter-high, rollable table that we used for snacks and drinks during our occasional football, holiday, or anniversary/birthday gatherings. The table sat in an open space between the living room and the formal dining room. Yes, we had dining room furniture by then.
The track on that square panel of drywall was little more than a circular loop of 18 in radius, sectional, steel track on cork roadbed. True to the notion of wintertime craft, I packed everything away before St. Valentine’s Day the following February.

The autumn of 2016 rolled around, and I planned a new seasonal layout. This time, the baseboard was a lauan door that we had replaced during the remodeling and that had not yet made it to the landfill. It was approximately 7 ft x 3 ft, which provided more track and display area than the drywall panel of the previous year, i.e., 21 sq ft versus 16 sq ft. The party table was again the support for the layout baseboard.

By 2017, I realized that designing the track pattern by the trial-and-error method of placing physical track sections together on the baseboard and hoping that loops would close and so forth was time consuming and frustrating. Therefore, I downloaded open source track planning software from the internet to aid in the design of a layout. That software greatly improved the efficiency of laying down the track, an important consideration for my temporary layouts. Using the track CAD software was almost as much fun as building the physical layout.

About this time, I gave up on using the party table as benchwork, and I invested in a pair of folding plastic sawhorses with adjustable length legs. A plywood baseboard, which sat on a skeleton of two 2x4 spines and six 1x2 ribs on top of the sawhorses, replaced the lauan door. What happened to the party table? The adjustable sawhorse legs allowed the new style of benchwork to be high enough that the table could be rolled under the train display after the sub-board wiring was completed. The table was then ready to be rolled out should it be needed for entertaining.
Something to keep in mind here is that I had a seasonal craft. I had no plan to build a permanent layout. I needed to be able to assemble the benchwork, lay track, and build out scenery and trackside industry items in a smooth and steady process. I needed to be able to disassemble those same items in a similar manner. As an example, the benchwork pieces were fastened together with screws that were inserted and removed easily with my electric drill. The pieces were all drilled and marked, and I kept the screws in a plastic bag and stored them with the other layout hardware. Attaching the ribs to the spines and the baseboard to the ribs took no more than thirty minutes. I kept the wooden benchwork items organized such that they were easily stored from one year to the next. Items not in a long-term storage situation were readily available for other purposes. The folding sawhorses, for example, were easy to hang on ladder brackets on a garage wall, and they found various uses during the non-train seasons.
The power and control of the wintertime craft layouts were traditional analog DC. I knew of DCC, as I mentioned above, and I thought that digital control of my locomotives would be an interesting step forward at that time given my hobby and professional interests in electronics and computers. Through a local hobby store with a sizable model train department and seemingly knowledgeable staff, I investigated converting from analog DC to DCC. I was put off by the apparent entry level costs. In the process of conversion, I would have to purchase one or more DCC locomotives plus the AC power supply and the control unit. The cost to switch, depending on the options, quickly climbed above $300 and gained on $500. Basically, my legacy DC locomotives and powerpacks would become obsolete. To be fair, retrofitting one of my DC locomotives for DCC operation might have been possible and less expensive than purchasing a new DCC equipped locomotive, but, at the time, that was unknown territory for me.
I shelved the notion of migrating to DCC and planned to continue with traditional DC operations.
I do not remember just what happened next. Sometime in 2019, though, I came across the website for the Wifi Model Railroad, LLC, (LocoFi ) company. The website had promotional aspects to which I could readily relate. First was the basic LocoFi philosophy. The track would be used only for delivering power to the locomotive, a classic track function and something that it could do trivially. Digital control signals would not be superimposed on the power and sent through the tracks as in DCC and in variants of its predecessors. By adding a decoder board to my locomotive, a process analogous to changing a locomotive from DC to DCC operation, as I now know, control of the movement of the locomotive and the sounds from the locomotive would be through modern wi-fi communications with the controlling device being either my cell phone or my tablet.
The basic LocoFi philosophy was not exactly new. Some predecessors of DCC as far back as the 1950’s had included designs with locomotive control provided by radio signals transmitted from a control console to a receiver and decoder mounted in a steam locomotive’s tender or in a boxcar. Some of those systems included locomotive sounds. In those early days, control circuitry was all analog and, even with transistors and early integrated circuit (IC) chips during the 1960’s and 1970’s, circuits were still large and power-hungry by today’s standards.
In assessing the LocoFi offering, I realized that my track could still be powered by my analog DC powerpack, i.e., not a new AC unit as required by DCC. Further, the LocoFi website actually showed a detailed video on how to install their Generation One decoder board in a locomotive similar to my Athearn Blue Box GP38-2, which I had purchased during the 1990’s modeling episode. Yes, I would have to purchase the decoder board for approximately $100, and, yes, I would need to add a $5 electrolytic filter capacitor to the DC output of my analog powerpack to provide the clean DC power for the decoder board in the locomotive. Neither installing the decoder in the locomotive nor adding the filter circuitry seemed daunting with my background in electronics and computers.
I built my 2019 seasonal layout with my traditional analog DC mentality, and I was using my switching locomotive for pulling the train, switching cars, and so forth. Power and control on the layout were from one of my two powerpacks from the 1990’s. Having ordered the LocoFi™ decoder board, I set the Athearn Blue Box GP38-2, the green Burlington Northern locomotive in Photos #5 and #6 above, out on my craft table along with my soldering iron and other tools and a roll of solder and other supplies. When the board and the LocoFi-provided supplies arrived, I
hastily began the installation process. I had the LocoFi installation video playing on my tablet on my worktable, and I followed every step.
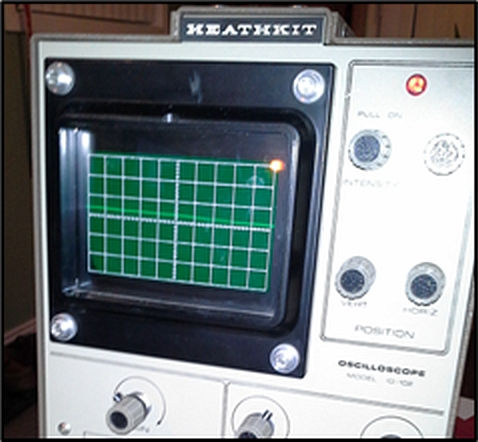
I had everything on the decoder board wired up, and I balanced the decoder board precariously on top of the motor. I placed the locomotive without its shell attached on a short piece of track in front of me on my craft table. I connected my second analog DC powerpack to the track using temporary clip leads to connect the powerpack, capacitor, and rails. Fortunately, I have an oscilloscope, and I was able to monitor the condition of the now clean DC power going to the rails. A quick check of the voltage on the rails with my voltmeter showed something in the vicinity of 15 V DC, and the oscilloscope showed a flat, ripple-free horizontal line across the screen, perfectly conditioned power for the LocoFi™ decoder board.
I established communications between my tablet and the decoder board using the LocoFi™ app and the optional direct wi-fi connection, the simplest option. I went through the nominal setup routine. The horn and the bell sounded. I tried starting the motor. The motor sound came on. I advanced the throttle control a little, and the locomotive started to move down the short track. Not surprisingly, the decoder board fell off of the top of the motor. I stopped the locomotive and reversed the direction of the locomotive with the direction control icon on the display on the LocoFi™ app. Advancing the throttle control a little, the locomotive moved the few inches back to its starting position in front of me.
That was certainly encouraging. I decided to move the locomotive with the dangling decoder board to the already functioning loop on the layout table. I disconnected my first powerpack from the track and connected my powerpack with the external filter circuitry to the track. Things seemed to go nominally for a few minutes of short moves back and forth along the front straightaway of the loop even with the precariously balanced decoder board on top of the motor. Then, I smelled smoke. I had encountered overheated electronics often enough over the years to know the distinctive aroma.
The decoder board was toasted. I made my situation known to the LocoFi customer support folks. They considered the original board to be still under warranty, and they sent me a new board to replace the initial board. I felt somewhat bad about that because I was sure that the failure was the result of something I had done though I did not really know what I had done.
In the replacement process, the customer support person wanted some details to help him understand what might have gone wrong and to guide him in providing me with mentoring so that I would be successful in installing a second board. This was the start of a long and beneficial relationship with LocoFi customer support, a relationship that has helped me to become a better modeling technician. Perhaps my communications with the support desk have provided the LocoFi team with insight into what can go wrong in the field.
To this day, I do not know what happened to cause that first installation to fail. Clearly, some exposed wire had come into contact with some other exposed wire. With the new board in hand, I did not want to make the mistakes that, by then, I was beginning to suspect that I had made during my first installation attempt. The first and most obvious item was soldering.

I had used my venerable low power, fine-tipped soldering iron during the first installation. That iron had served me well in many electronic projects over the years where soldering small wires together, soldering components onto circuit boards, and attaching wires to cable connectors was involved. However, installing the LocoFi™ decoder board involves soldering wires to “sizable” pieces of metal on the locomotive frame and motor. I can believe that the little iron just did not have enough heat to yield a good mechanical and electrical connection. Perhaps, during my back-and-forth test runs, a marginally connected wire came loose and touched a sensitive spot as a result of the bouncing around that the decoder board did while sitting on top of the motor.
The installation of the LocoFi™ decoder board on a classic Athearn motor involves soldering one wire (orange) to a copper clip on the top of the motor and another wire (gray) to the corresponding clip on the bottom of the motor. For the top connection, I left the copper clip connected to the plastic of the motor housing and soldered the orange wire from the decoder to that strip of copper. Because of the size of the copper strip, some time was required to get it hot enough to melt the solder and to make the connection. In the process, the plastic to which the copper strip was clipped softened and deformed a little. The copper clip, to this day, does not snap into place as it did when the motor was new.

Fortunately, having seen the plastic deformation problem for the top motor clip, I took the bottom clip off of the plastic motor frame before soldering. Still, the process was slow and somewhat sloppy because of the relatively low heat and low tip mass of my iron compared to the mass and surface area, i.e., heat radiating area, of the copper strip.
Recognizing the difficulties that I had experienced with soldering, I asked LocoFi customer support for advice on their soldering tools and techniques. They recommended a particular brand of soldering station, but many good ones are on the market. Over the years, I had never used a soldering station, but I took the opportunity to acquire one before starting the second installation. The LocoFi installation video suggested a temperature setting for the soldering wand. I discovered as I went along with the second installation that the suggested temperature was too low for the solder that I had. My venerable soldering iron then had two strikes against it, i.e., the mass/surface area of the metal pieces and the apparently high melting point of the solder that I had on hand.
To be sure, the control board has seven wires that need to be soldered plus a jumper wire is needed between the front and rear trucks in my particular locomotive, i.e., not very much soldering at all. With the right tools and supplies and a clear understanding of what needs to be done on any given locomotive, the wiring phase of the decoder board installation should probably not take more than an hour. The more mechanical aspects of an installation, however, can vary widely from locomotive to locomotive based on the videos on the LocoF™ website.
I had the second board wired up for the start of my 2020-21 winter season layout. This time, I used some blue-tack adhesive to steady the board on top of the plastic frame of the motor. I felt pretty good about my installation work. The new soldering station had lived up to expectations, and I had not melted any more plastic. I was ready to test the locomotive on that year’s track loop. Everything seemed nominal. The blue-tack goo held the board in place. It was time to place the shell of the locomotive back onto the frame, i.e., over the motor and the decoder board, and to get on with running my train.
The shell just would not go back into place. As I would slide the shell over the motor, the decoder board would pull loose from the tacky stuff, and the board would be floating inside the shell. I do not know what else might have been happening. The result was that the second board failed.
Like the first failure, I felt that the problem was on my end. Nevertheless, customer service asked me to return the damaged board, and they credited my account. I considered walking away from the wi-fi experiment and staying in the analog DC realm. Both LocoFi and I were disappointed at this stage. I was disappointed in myself for somehow not having the patience, the skill, the tools, the modeler’s insight, or whatever to accomplish what appeared on the surface to be a straightforward process and one that the LocoFi folks had demonstrated in one of their online installation videos. I want to be clear. The two installation failures were entirely on my end. LocoFi had a lot of decoder boards in use by that time, and few, if any, failures like mine had been reported.
I put the GP38-2 back together for DC operation. The winter 2020-21 winter craft season passed with my using my two locomotives for running trains with traditional analog DC on blocked tracks.
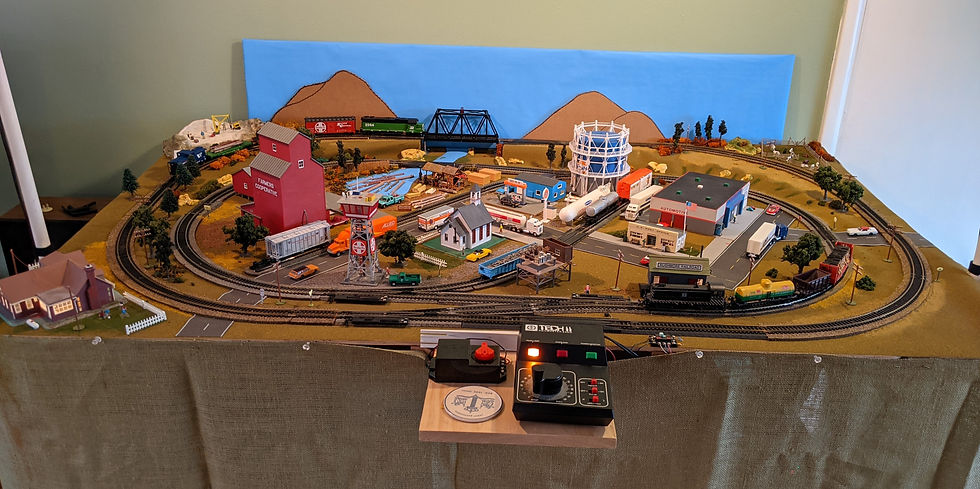
As life went on and the covid restrictions of 2020 were waning in the spring of 2021, I learned that my brother-in-law, who harbors a latent interest in train modeling, was coming to visit my wife and me in Montana in the early summer. I decided that I would get the train paraphernalia out of its usual nine-month hibernation and that I would take the brother-in-law through the full seasonal train model buildout during his visit.
By then, I had learned that LocoFi was delivering its Generation Two decoder board. It was slightly smaller than the version one board. In my communications with customer service, I had shared numerous caliper measurements defining the inside dimensions of my locomotive shell and dimensions of my motor height and width to 1/1000 of an inch (1 mil). My wife had truly surprised me with the gift of a digital caliper that preceding Christmas. LocoFi customer service assured me that, while the original board should have fit inside of my shell, the new, smaller board surely would fit.

Perhaps as important as the slightly slimmer board, LocoFi had just developed a 3D printed platform designed specifically for the classic Athearn Blue Box motor. The platform would snuggle around the motor’s plastic frame and hold the microcontroller, sound, and wi-fi components of the decoder board on one end of the platform and the speaker on the other end of the platform. The platform had holes through which the seven color-coded wires could be passed thereby helping to guide them to their appropriate places and to keep them tucked out of the way of the drivetrains and the interior sides of the locomotive shell. While I could not see inside of the locomotive shell during my attempts to reattach it, I am sure that some wires moved around thereby potentially leading to some of the issues that I had encountered.
I purchased the Generation Two decoder and the mounting platform. I was not daunted by my previous two efforts. I was, and still am, sold on the concept of separating the power and the control functions, i.e., making use of my existing DC components with relatively low-cost modifications, and using a control surface and communications medium that I already had. I just had to try one more time. I went through the installation motions yet another time. This time, I did not toast the board.
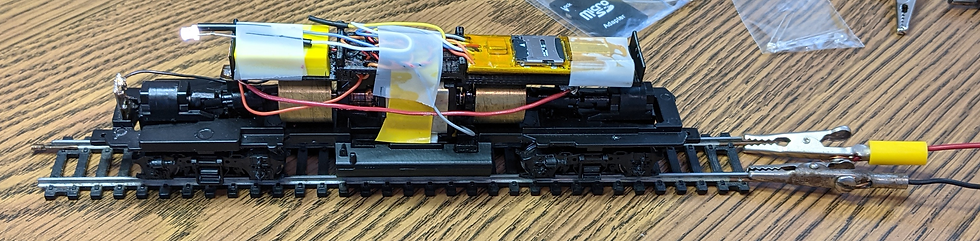
However, with my handling of the locomotive frame and motor and the decoder board, I managed to break a wire off of the edge of the decoder board. I do not know how that happened, too many times tucking the wire under this and around that, I suppose.
I knew that I did not have the skill to reattach the tiny loose wire to the edge of the decoder board. LocoFi support came to my rescue yet again. They said to send the board back to their shop, and they would reattach the wire. In the process, they tested the board to make sure that it was still in factory new condition. Given my history, they were not taking any chance that I had already damaged yet another board. Before returning the board to me, they placed the decoder board and the speaker on the mounting platform and locked them in place with wraps of Kapton® tape. They routed the seven wires through their suggested holes knowing that I had the Athearn Blue Box GP38-2, as they had in their own stable of locomotives.
As I reflected on the broken wire incident as I was writing this, I recalled that during that period of testing on my summertime loop, the locomotive, without a shell, would, occasionally, just stop. LocoFi support suggested that a wire might be caught in the drivetrain or between a flywheel and the motor frame, i.e., some mechanical problem. Neither of those ideas seemed to fit. In my reflection, I wondered whether either the orange or the gray wire, the ones that actually power the motor, was loose at the decoder board connection, i.e., the wire might vibrate into one position for a while making contact with the board and then vibrate loose thereby losing its connection with the result that power to the motor would drop out. Indeed, it was the gray wire that needed to be reattached..
By the time that the repaired board came back to me in the late summer of 2021, my brother-in-law had returned to his home, and the off-season layout had been disassembled. At that time, my wife and I were in the midst of moving from Montana to Washington. I placed the locomotive plus the decoder board and platform in the original Blue Box, and I set the box in the top of one of the moving boxes, i.e., I wanted it to be the first thing out once we got settled in Washington. The winter season of 2021-22 in Washington came and went, but I did not attempt my wintertime craft that year. We still had half-emptied, even some unopened, moving boxes in most rooms. Our new house was smaller than the Montana house, and I was not sure just where I could place a layout, anyway.
A year later, well into the autumn of 2022, the moving boxes had all been emptied. Though the date was later in the fall than I usually started the wintertime craft, my wife suggested that I build out the model train display in an alcove at the head of the stairs outside of the door to a bedroom that was repurposed to serve as my craft/hobby room. I measured the available space in the alcove, launched the track planning software, and came up with a design for a layout in the new space. The new space is smaller than the space I had used in the Montana house. I got out the folding sawhorses and the benchwork items that I had moved. The benchwork items needed a little trimming to fit the new space, but I got the new baseboard built and a loop of tracks laid.
My main objective, however, for the 2022-23 wintertime craft season was to get the LocoFi™-equipped locomotive fully functional. LocoFi customer service had been so supportive of my efforts for three years that I owed them, as well as myself, a successful conclusion. I mentioned above that the soldering station had been an important addition to my toolbox. I decided to acquire a third hand tool (not a third, hand tool but a tool called a third hand), and LocoFi customer support suggested some options based on their experiences. I had been using a small, tabletop vice for holding the decoder board, motor clips, and wires during soldering, but the jaw of the vice was just not as accommodating as the alligator clips and universal joints on the true third hand device.
I took a cue from the original installation video, and from the condition of the returned board and mounting platform, to use Kapton® tape for corralling wires and for making other attachments. I had not given tape much consideration with respect to the overall decoder board installation. I had lots of vinyl electrical tape on hand, and I just used that. The vinyl tape that I was using was approximately 6 mils thick. Having made a lot of caliper measurements, I realized that when I was dealing with clearances of a few thousandths of an inch, the thickness of a couple of pieces of vinyl tape could add up and pose a problem with the fit of the shell.
Therefore, I purchased a package of Kapton® tape with four rolls each of different widths. The four different widths provided options for insulation and tacking down wires and so forth. The Kapton® tape is just 1 mil thick. Kapton® film was extensively used by NASA in the Webb space telescope, i.e., it is good stuff.
In a case in point, I had used vinyl tape to insulate the locomotive frame from the underside motor contact clip as in Photo #10 above. In the third installation, I replaced the 6-mil thick vinyl tape with the 1-mil thick Kapton® tape. With this replacement, I reduced the overall height of the motor and decoder board assembly by approximately 5 mils. During the third installation, I realized that the underside motor contact had a small blob of excess solder. I carefully removed that with a solder wick. Removing that excess solder might have provided another mil or two reduction in the finished height of the motor and decoder board assembly. Little things like this might not matter in many electronic or modeling efforts, but they seemed to be important to consider and to deal with in this case.
The solder wire that I had on hand had a diameter of 2 mm. In addition to the mass of some of the locomotive frame and motor parts, that size of solder wire took a lot of heat to melt, i.e., strike three against using my old soldering iron. The third thing that I ordered before attempting the third installation was a new roll of solder with a 1 mm thick wire. 0.5 mm diameter might have been even better for this project. Nevertheless, the new solder melts readily in the steady heat from the soldering station.
By this time, I knew where every color-coded wire extending from the edge of the decoder board needed to be attached. Honoring a hint from customer service, I cut the various wires as short as I could to allow the wires to reach between the decoder board and their respective destinations and still have enough slack in the wires for moving the board around while working with other wires. Then, I used the Kapton® tape to tack each wire down to the motor so that each wire was out of the way of the drivetrains and the space on the sides of the motor through which the shell had to pass.
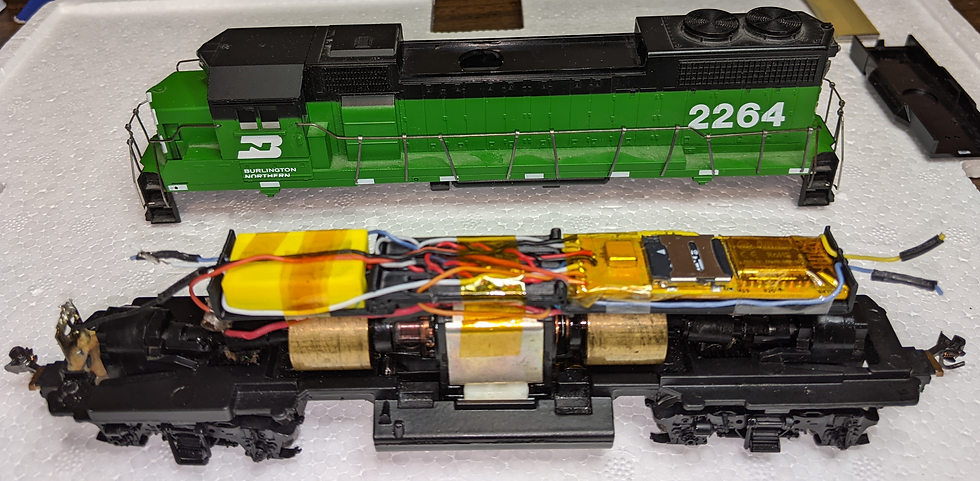
After all of the wires were routed through the mounting platform holes and carefully soldered using the fine solder wire, I set the platform on top of the heat-deformed plastic of the motor frame. The platform would have fit snuggly had I not damaged the plastic in my rush during the first installation. Using another tip from customer support, I positioned the platform as well as I could over the irregular plastic and locked the board and platform assembly in place with a length of Kapton® tape. I used the widest tape in the pack that I had purchased. That piece of tape crosses over the assembly and attaches to each side of the motor. It takes some space on the sides and a bit on the top of the motor, but less than vinyl tape, and the taping is definitely more structurally stable than using blobs of the tacky blue stuff.
I tested the assembly on my small worktable track, and all seemed in good order. I decided to try to reattach the locomotive shell. This step had been a significant problem at one point in this process. My use of vinyl tape had probably been a defining factor. This time, however, with a minor condescension, as I will discuss later, I was able to slide the shell almost trivially into its proper position such that it actually locked to the frame.
I took the locomotive to my embryonic seasonal layout. The loop was composed of traditional nickel silver sectional track nailed through cork roadbed with the nails bottoming in the plywood baseboard. With years of experience, I knew to check each section joint to be sure that the rail ends were properly slipped into the joiners. I had more than one point at which I attached power to the tracks in order to minimize the effects of dirty tracks and the odd joiner that did not do its job in the DC world. I was reasonably confident that I had a good loop for testing the locomotive that was apparently, successfully LocoFi™-equipped.
By this time, I had set aside my old analog DC powerpack with the external filter capacitor, and I was using a small 12 V, 12 Ahr emergency battery for powering the track. That was a matter of convenience. The battery, with a handle, was easily moved between the test track in my craft room and the loop on the layout board in the alcove. The battery has a built-in voltmeter to monitor the battery’s charge, and it has an on-off switch for easily killing power to the track/decoder board after running my train, or in a malfunction.
I fired everything up. The horn and bell sounded. The engine started up, and the locomotive started to move. So far, so good. Sadly, the locomotive did not go far before the sounds stopped. I could still control the speed of the locomotive, and I brought it to a stop. I killed the power to the locomotive and wondered what this situation indicated. Another email to customer support resulted in a suggestion to reformat the SD card that holds the sound files and to reinstall the sound files. That seemed to cure the problem of dropped sounds.
Customer support also reminded me to be sure that I had clean track, i.e., the sound cutting out was a symptom of the decoder experiencing a momentary power drop. I tried wiping the tracks with isopropyl alcohol and with a cloth dampened with electronic contact cleaner spray. That made a small difference, but not one that I could count on around the entire loop or on an industrial siding. The decoder board would still lose power at random locations on the track. These were different from the momentary drops that had affected the sounds. The locomotive would be dead on the tracks. Only a cold reboot of the entire system would allow me to start the locomotive again.
Occasionally, the locomotive would make a complete lap around the track loop. When I got lucky in this way, I would increase the speed such that the power drops were not critical, i.e., the on-board capacitor would hold the power for the decoder up until power from the tracks was restored. Part of my logic here was that letting the locomotive run might wear tarnish off of the tracks and wheels, but I do not think that much, if anything, was gained by this tactic.
I decided to pull up all of the neatly nailed sectional track and purchase new Bachmann E-Z Track®. My logic was that new track should not suffer from odd bits of tarnish on rails and between rails and joiners such as the 25+ year old track sections might have had.

Still, with the new track, I got erratic behavior from my locomotive. I was confident that the problem was not an installation issue, and dirty track would seem to have been obviated. Yet, I had some issue of power delivery to the decoder board. I wondered about the wheels. I took the locomotive back to my worktable and studied the wheels under a bright light and a magnifier. Indeed, here and there were small blobs of tarnish. As with the new tracks, I gained some performance benefit after trying to clean the wheels, but I would still get power drops.
Finally, one morning, I woke up with the idea that maybe the inside surfaces of the flanges on the wheels were not making good contact with the wipers that led to the power wires for the decoder board. I recalled that I had purchased a package of model train lubricants a few years earlier and that one product in the package was labeled as conducting to be placed on the motor brushes. I thought that a drop or two of the conducting lubricant would not hurt the flange to wiper contacts. .
Indeed, not having continuous contact between the flanges and the wipers would seem to have been the last loose nut. In fact, it may well have been the most significant culprit underlying the power supply issue all along. Maybe my carefully nailed down sectional track, wiped with solvents, was good enough after all. Maybe I could have saved the money on the new track, though I do like its ease of assembly, which is a factor in the wintertime craft philosophy, and I like the uniform look of the roadbed. Then, I remembered the old admonition of not placing the layout on a floor, particularly a carpeted floor. Maybe that episode from the early 1990’s came back to haunt me after all. I shared my apparent success with customer support and by return email, I was told that the conducting lubricant idea was discussed in item #3 in their troubleshooting tips for curing power drops. I was surprised, and a bit embarrassed, that I had missed that on the website.
The locomotive was running fine at this point. However, during this installation, I took some shortcuts and made compromises in order to speed up getting the locomotive running on my layout. In Photo #14 above, you can see that the headlight wires are terminated with heat shrink tubing, i.e., I had not attempted to attach the LED headlight/cab light assembly. I figured that I could live without the light. In an attempt to help you to understand my thought process, I am including an exploded diagram of the Athearn locomotive shell.

With the decoder board mounted on top of the motor, the shell would not slide into place and lock onto the frame. While I could not see inside the shell, in studying the exploded diagram, I imagined that the speaker extended through the opening, i.e., the red-outlined yellow box in the exploded view, in the main part of the shell just enough to block the back side of the Cab Windows insert, i.e., the red box on the Cab Window piece.
In the first shortcut, I pried the Cab and the Cab Windows out of the shell and slid the clear plastic windows piece out of the Cab. It was not cemented in or locked in with tabs. I reattached the Cab to the rest of the shell and tried to connect the shell to the locomotive frame. As I mentioned earlier, the shell did slide relatively easily into place and lock to the frame. At that moment, I was more concerned with getting the locomotive running on my layout, and I did not worry about the light, i.e., a bit of a compromise or taking a shortcut.
However, after the sound and the power dropping issues were handled, I wondered whether I could attach the light in the open space inside the cab. I was encouraged to do so by LocoFi™ support but warned that installing the light could be a challenge, i.e., one of those locomotive-specific, mechanical issues that I mentioned above. I was reasonably sure that I knew what to try. I would use my razor saw to cut out the area of the red box in the back of the Cab Window piece. That was easily done. With the window reinserted into the Cab and the Cab reattached to the shell, the shell still slipped over the motor and locked to the frame.
I could have quit there. At least, I had the windows back. However, I decided to evaluate the light one more time. The blue and white wires had been routed from the decoder circuit board past the speaker and through a pair of holes on the front of the mounting platform. The LED had been prepared with lengths of blue and white wire to provide flexibility in where the light was placed. After some study and, perhaps, a coin toss, I decided to remove the Cab/Windows assembly from the shell again and mount the LED in the top of the Cab holding the light in place with hot glue. With the LED glued into place, I reattached the Cab/Windows piece to the rest of the shell. I did a fit test to be sure that something unforeseen was not preventing the shell from attaching to the frame. Passing the test, I then had to solder the LED blue and white wires to their respective mates with the shell flopping around next to the rest of the locomotive. That was a bit of a challenge, but I got it done.
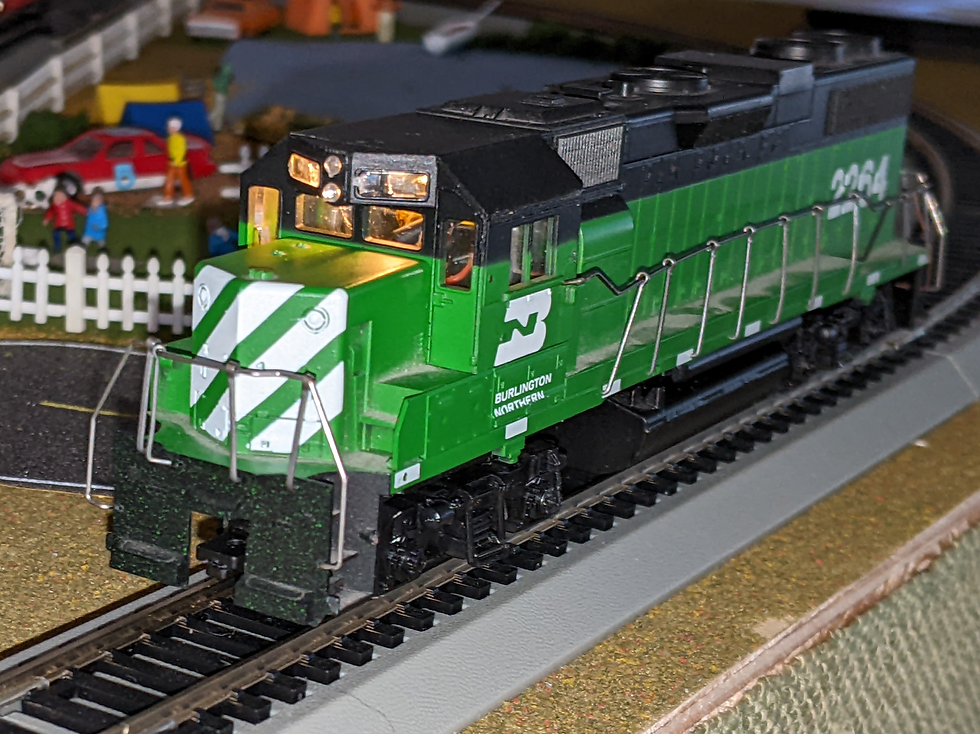
I placed the locomotive on my layout to test the light. The light worked as expected, and in the process of installing the light, I did not seem to have disturbed any other aspect of the installation.
Now, my old DC locomotive, outfitted with the Generation Two LocoFi™ decoder board, seems to be working just as I had expected several years ago when I started this process. I was successful in large part as a result of the untiring mentoring of LocoFi customer service. However, the path might have been shortened if I had been a little more patient, if I had taken time to better understand the scope of the project through reading and re-reading the installation and troubleshooting tips and watching the videos on the LocoFi website, and if I had made sure that I had suitable tools and supplies for the project.
I do not suppose that the LocoFi™ philosophy and devices will replace DCC. The LocoFi™ philosophy and devices, however, might form the basis for another viable standard for the powering and control of model train locomotives and accessories. For now, for a person with legacy analog DC equipment, the LocoFi™ decoder board provides a convenient step from analog to digital control of locomotives and for adding engine, horn, and bell sounds. In my case, I was modernizing my layout power and control, and that modernization was relatively inexpensive by integrating the LocoFi™ decoder board into existing hardware. One can only imagine future wi-fi decoders to control other features of a model train layout.
About this time, I should close with something like “lived happily ever after.” Actually, this being late January and my having satisfied my primary objective for the seasonal craft with getting my locomotive fully operational with the LocoFi™ system, I am thinking about disassembling the layout for this year. Looking farther ahead, I hope to have more seasonal layouts with my LocoFi™-equipped GP38-2 pulling trains and dropping and picking up cars on industrial sidings. I would like to convert another locomotive, for example, a switcher, to wi-fi control, so that I could operate both the switcher and the general-purpose locomotive simultaneously. I certainly will be watching the LocoFi website for new products that might complement my wintertime craft.
LocoFi™ indicates a trademark of Wifi Model Railroad, LLC.
LocoFi indicates the Wifi Model Railroad, LLC, company itself.
E-Z Track is a registered trademark of Bachmann Industries, Inc.
Kapton is a registered trademark of E. I. du Pont de Nemours and Company.

April 2025
I made a few edits to the 2023 post of this story. The Forum administrator suggested I add the video of the converted locomotive here.